Introduction
In the competitive world of perishable goods, maintaining consistent quality and freshness is non-negotiable. Customers judge produce not just by its taste but by its visual appeal and texture in-store — critical factors that determine supermarket success. Behind the scenes, cold chain management ensures this standard is met, but it’s a complex, multi-step process fraught with challenges.
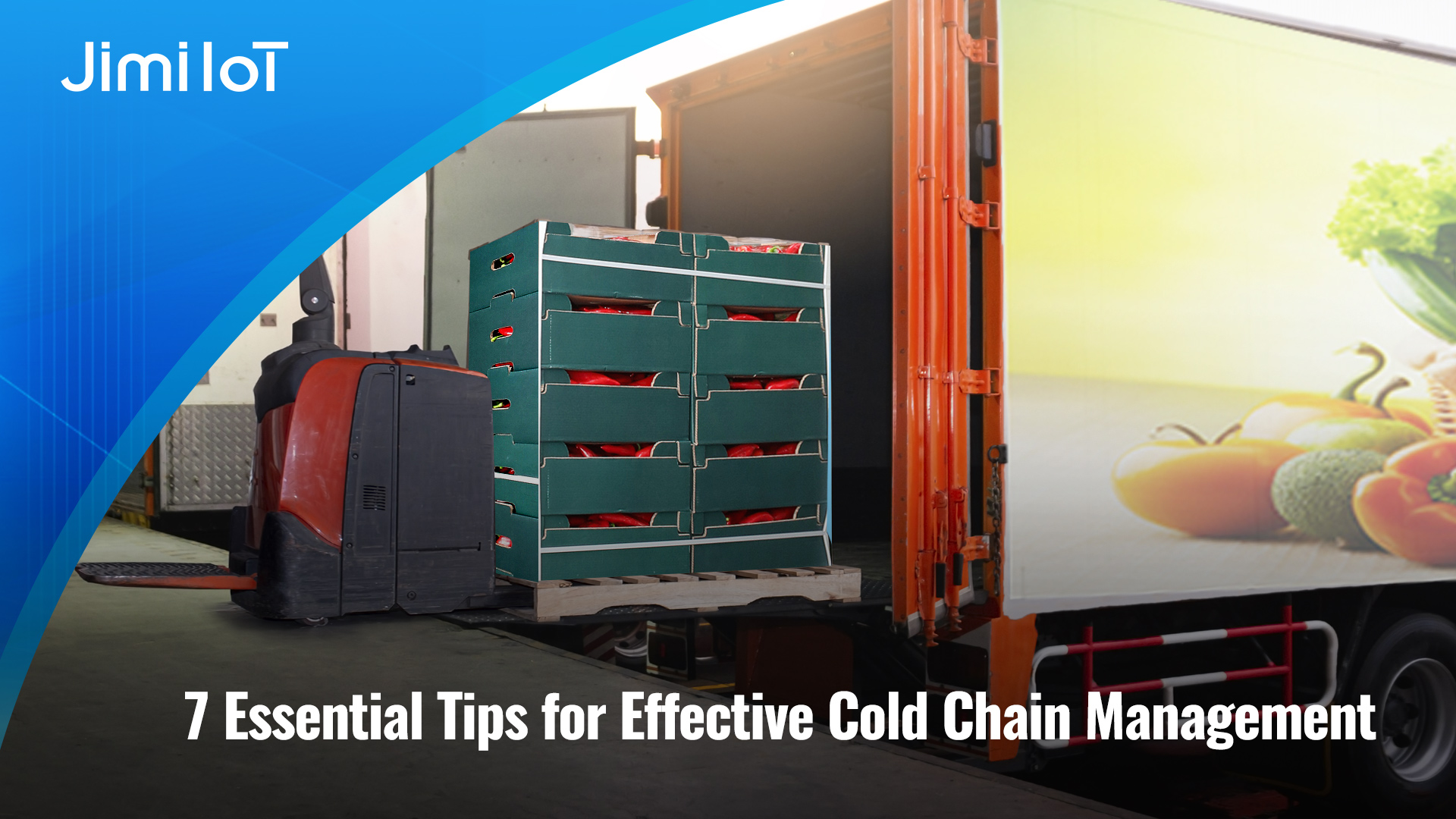
From harvest to the retail shelf, temperature management is the linchpin of a successful cold chain. The smallest deviation can mean the difference between a shipment of fresh, safe produce and spoiled, unsellable stock. For example, fresh vegetables like lettuce require storage between 32-39°F to maintain an optimal shelf life of up to 15 days. Just a slight increase can halve that lifespan, leaving stores with less time to sell or forcing waste.
At Jimi IoT, we understand the stakes of cold chain logistics. Our advanced IoT solutions empower businesses to maintain precision across every step of the journey, ensuring temperature consistency, compliance, and quality assurance. The following seven tips provide actionable strategies for more effective cold chain management.
- Pre-Cool Products After Harvest
Pre-cooling immediately after harvest ensures that perishable goods enter the cold chain at the correct temperature. For example, fruits and vegetables should be cooled to their ideal storage range (e.g., 32-39°F for many fresh produce items) before being loaded onto refrigerated transport. This step reduces the thermal load on refrigeration units during transit, preventing temperature spikes that could compromise freshness. Proper documentation of initial temperatures during pre-cooling is also essential, as it establishes a baseline for quality assurance throughout the supply chain.
- Inspect and Maintain Transport Insulation
The insulation of refrigerated trucks and trailers is critical for maintaining consistent temperatures. Over time, wear and tear can degrade insulation materials, leading to heat transfer from external environments. Studies show that older trailers can lose up to 50% of their insulative efficiency within a decade, significantly increasing risks during transit. Routine inspections for cracks, gaps, or compromised seals, combined with timely maintenance, can mitigate these risks. Insulation upgrades or using modern refrigerated units with advanced thermal protection can also improve performance.
- Operate Refrigeration Units in Continuous Mode
Continuous mode operation is essential for maintaining precise and stable temperatures throughout the transport process. Some operators may switch to “start-stop” or “fuel saver” modes to reduce fuel consumption; however, this creates temperature fluctuations that can damage sensitive goods. Regular calibration of thermistors and refrigeration components is equally critical to ensure that readings and system responses align with setpoints. Using well-maintained equipment that delivers consistent cooling can significantly extend product shelf life.
- Ensure Proper Pallet Loading for Airflow
Efficient airflow within refrigerated trailers is necessary to distribute cold air evenly. Pallets should be loaded to allow air circulation around and between stacks, avoiding direct contact with trailer walls, which can create hotspots or cold zones. The common “center-line” configuration, where pallets are spaced slightly away from the walls, promotes consistent temperatures from the front to the back of the trailer. Loading guidelines should be strictly followed, and improperly loaded trailers should be corrected to prevent uneven cooling.
- Optimize Load Transfers and Receipts
The transfer of goods—whether during loading, unloading, or transshipment—is one of the most vulnerable points in the cold chain. Open doors and prolonged exposure to ambient temperatures during these transitions can lead to temperature excursions. To minimize risks, operators should streamline these processes by reducing idle times and ensuring quick and efficient hand-offs. Using insulated dock shelters and pre-cooled staging areas can further safeguard perishable goods during transitions.
- Inspect Trailers and Monitor Product Conditions at Every Transfer
Routine inspections of trailers and goods during every stage of the supply chain are vital for quality assurance. Trailers should be checked for cleanliness, odor, and contaminant-free conditions before loading, as residual issues from previous cargo can affect current shipments. For perishable goods, regular pulp testing or temperature spot-checks can confirm that products remain within the desired temperature range. Documenting these inspections provides accountability and ensures compliance with safety standards.
- Monitor Temperatures Continuously
Real-time temperature monitoring is a cornerstone of effective cold chain management. Data loggers, sensors, and tracking systems can provide continuous visibility into temperature conditions, alerting operators to deviations as they occur. These systems allow stakeholders to take immediate corrective action in the event of excursions, such as redirecting shipments or adjusting refrigeration settings. Over time, the data collected can also be analyzed to identify recurring issues, optimize carrier performance, and improve overall cold chain efficiency.
The Jimi IoT Advantage in Cold Chain Management
Managing a cold chain effectively requires innovative technology that ensures real-time visibility, accurate reporting, and immediate responses to potential disruptions. The LL309 Temperature and Humidity Monitoring Tracker is specifically designed to address the complexities of cold chain logistics, offering a robust solution to maintain the integrity of perishable goods throughout transit.
Effective cold chain management demanThe LL309 stands out with its advanced capabilities in precise location tracking, utilizing GPS, BDS, and LBS technologies. This ensures accurate and continuous monitoring of your assets, regardless of their location. Beyond location data, the device features a built-in temperature and humidity sensor, which tracks environmental conditions in real-time. Any deviation from the preset parameters triggers instant alerts over the 4G network, enabling operators to take corrective action immediately and prevent spoilage or quality loss.
In scenarios where connectivity may be temporarily unavailable, the LL309 is equipped to store up to 20,000 records of location, temperature, and humidity data offline. This stored data can later be exported via a Type-C cable for analysis, compliance documentation, and optimization of cold chain operations.
By incorporating the LL309 into your cold chain management strategy, you can ensure that every shipment arrives in optimal condition, reducing losses, enhancing customer satisfaction, and meeting stringent quality standards.
Conclusion
Cold chain management is an intricate process that requires meticulous planning, seamless coordination, and the right technology to succeed. By following these seven tips and leveraging Jimi IoT’s innovative tracking solutions, you can safeguard product quality, reduce losses, and exceed customer expectations in the perishable goods industry.
Stay ahead in the cold chain with Jimi IoT. Explore how our solutions can transform your operations today.
Why JimiIoT
JimiIoT is a global leader in innovative IoT solutions. We provide cutting-edge hardware and software tailored to enhance efficiency and connectivity. Our range of products includes advanced GPS tracking devices, asset management solutions, smart vehicle dashcams, and telematics platforms. With a focus on technological excellence and customer satisfaction, we empower businesses to optimize operations and gain valuable insights from data-driven analytics. Trust JimiIoT to drive positive change and unlock growth opportunities in the digital age.
If you would like more details, please visit Facebook, LinkedIn, INS, and Twitter pages for further information.